Pee Empro Exports Pvt Ltd is a well-established woven apparel manufacturer with a rich history in the textiles business. With a strong customer base including renowned brands like Gap, Old Navy, Anthropologie, and more, the company has a significant presence in both the US and EU markets. With a monthly capacity of 700,000 units that includes a diverse mix of adult and kids’ clothing, with a specialization in dresses, tops, skirts, and shorts.
Pee Empro Exports Pvt Ltd had been utilizing a prominent system, but encountered certain challenges along the way. In search of an alternative solution that could overcome these shortcomings, they eagerly adopted Stitch. This decision proved to be a game-changer as Stitch effectively addressed numerous issues, leading to exceptional results and significant progress for the company.
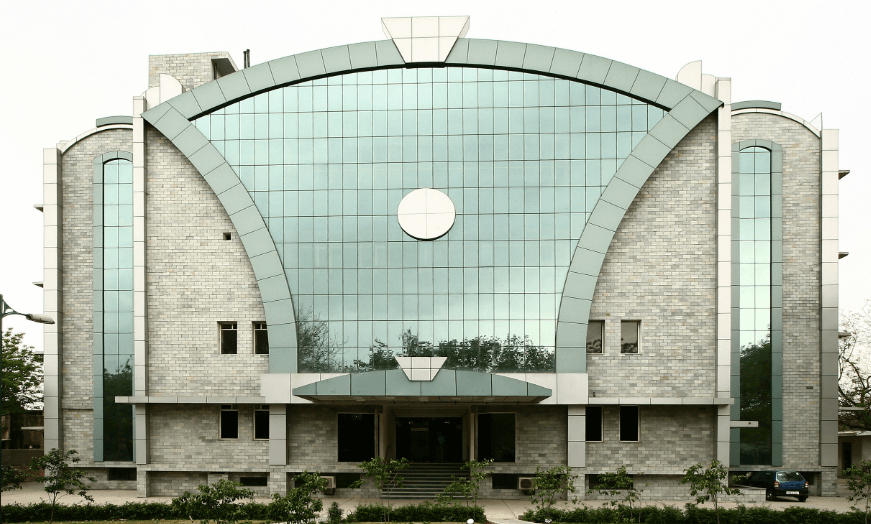
Problem Statement
Pee Empro Exports faced significant challenges in their manufacturing processes, primarily due to the absence of digitisation and real-time insights. This led to inefficiencies in vital areas like inventory management, centralized planning board, machine maintenance, and resource allocation. Let’s explore each challenge separately:
- Inventory Management- Pee Empro Exports faced critical inventory challenges with their previous system, lacking real-time visibility into stock levels, demand patterns, and supplier data. The combination of excessive carrying costs, frequent stockouts, and production delays resulted in significant impacts on their operations, including deadstock, completed orders, and aging of fabric.
- Planning Board- Pee Empro Exports encountered significant challenges resulting from the absence of a centralized planning board. This lack hindered their visibility into critical aspects such as tracking of purchase orders, monthly capacity, resource allocation, line-wise planning, accurate hour scheduling, real-time delay tracking, and pre-production insights.
- Operator Production Tracking- Monitoring and tracking individual operator performance on the production floor have been a manual and time-consuming process at Pee Empro Exports leading to difficulties in identifying skill gaps and performance bottlenecks.
- Scheduled Maintenance- Pee Empro Exports has experienced unexpected machine breakdowns, resulting in unplanned downtime and increased maintenance costs. Reactive maintenance practices have hindered productivity and led to production disruptions.
- Auto Cut Plan Generation- Pee Empro Exports faces material wastage and higher production costs due to manual cutting plans. There was a lack of a system that could reduce fabric consumption, meet optimum production requirements, and cutting constraints, resulting in limited cost savings and sustainability.
Solutions
1) Efficient Inventory Management- With Stitch, Pee Empro Exports gains real-time visibility into stock levels, demand patterns, and supplier data, enhancing inventory management. The optimized system minimizes excessive carrying costs, stockouts, and production delays, ensuring efficient and cost-effective inventory control.
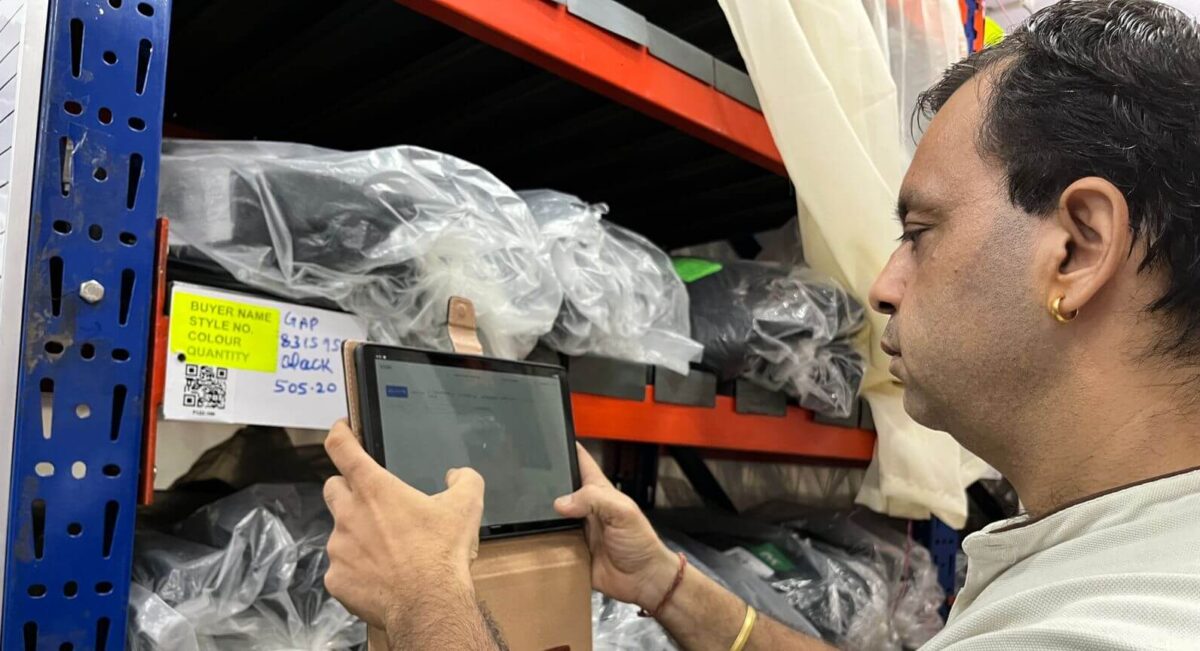
2) Enhanced Planning Efficiency with Planning Board- Pee Empro Exports now enjoys seamless resource management, purchase order tracking, monthly capacity planning, resource allocation, line-wise scheduling, accurate hour planning, real-time delay tracking, and pre-production insights, all made possible through our well-organized & centralized planning board.
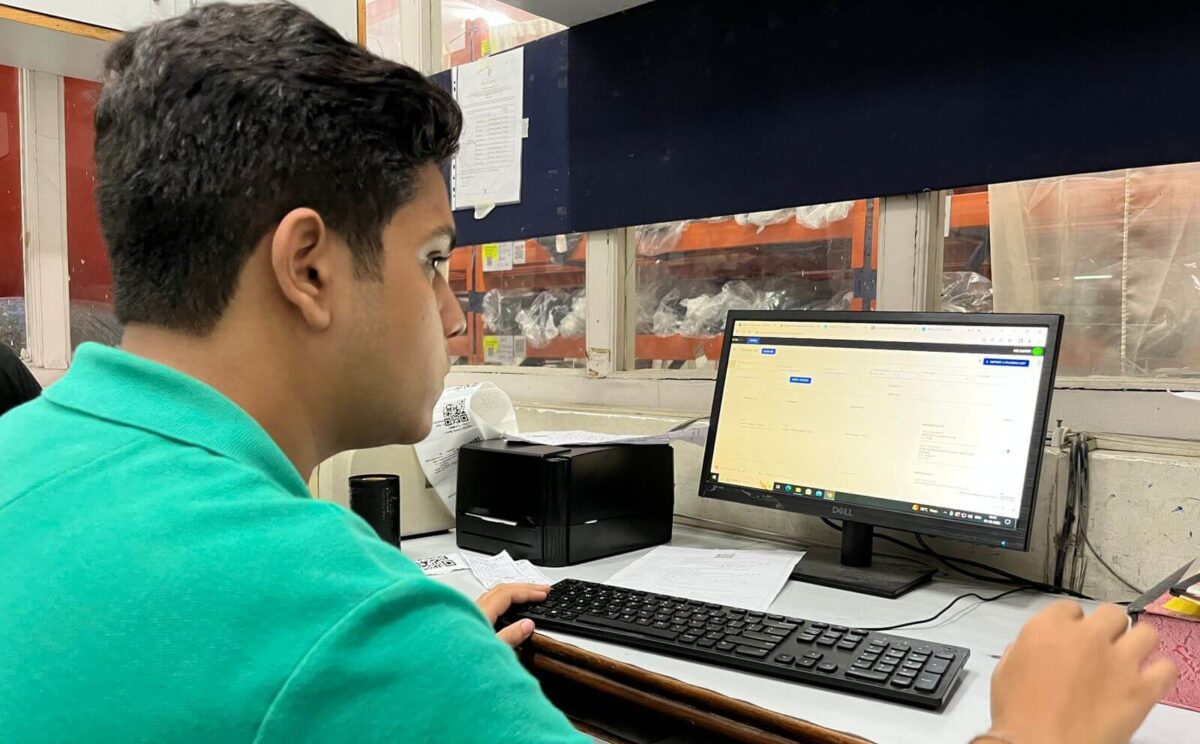
3) Easy Performance Monitoring- With Stitch, operator performance tracking on the production floor is automated, offering real-time insights into productivity and efficiency. Prompt identification of skill gaps and performance bottlenecks allows Pee Empro Exports to implement targeted training programs and incentives, boosting operator performance and productivity.
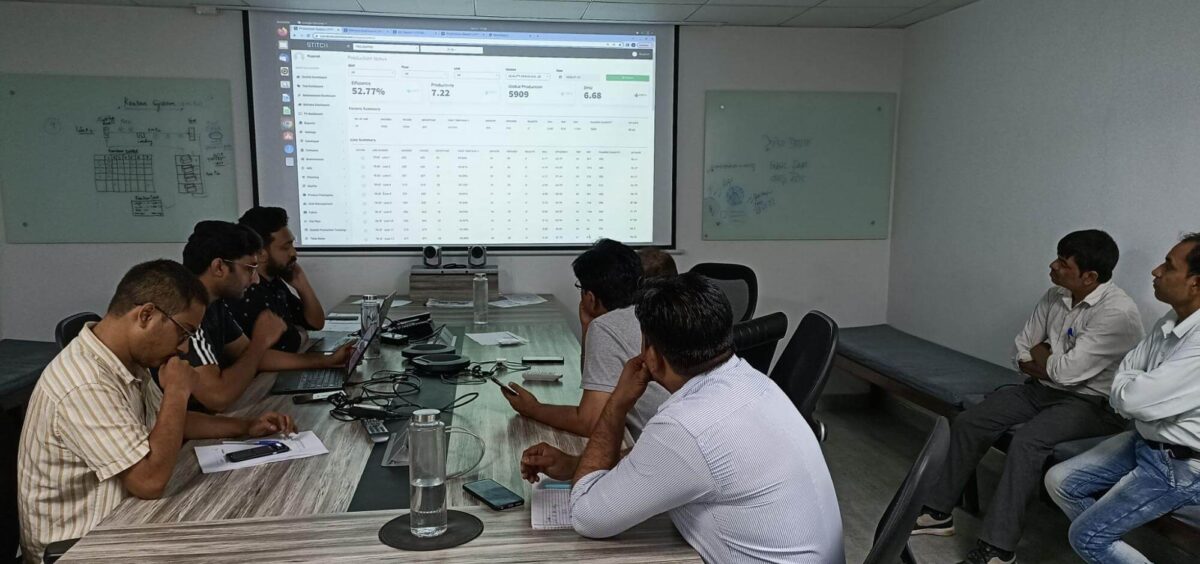
4) Smart Maintenance- Stitch facilitated maintenance, ensuring that Pee Empro Exports can proactively address unexpected machine breakdowns. By leveraging machine learning algorithms and IoT sensors, the system anticipates potential failures, enabling timely maintenance, and minimizing unplanned downtime, ultimately improving overall productivity.
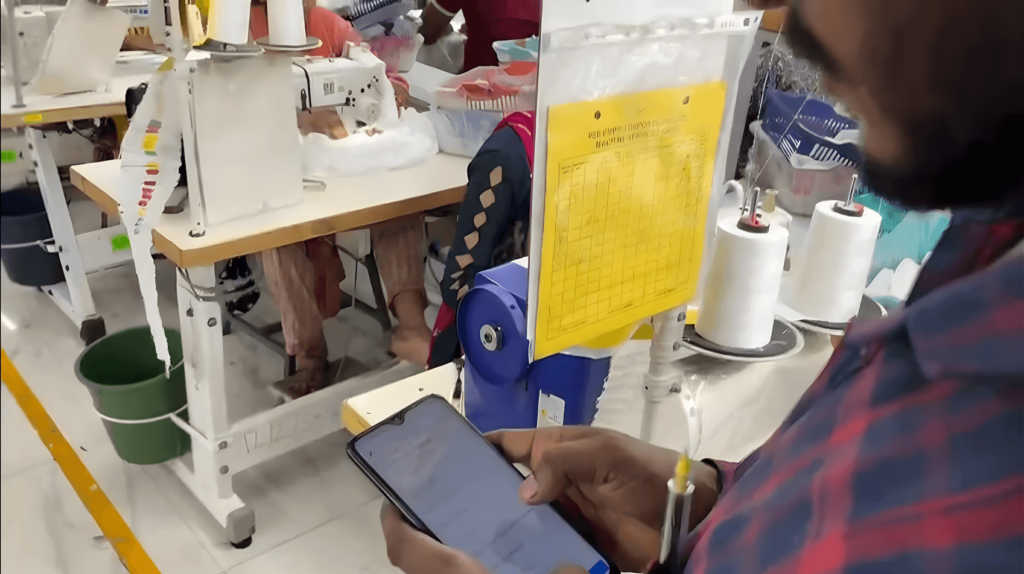
5) Auto Cut Plan Generation- Stitch optimized the cut plan generation process for Pee Empro Exports, considering material dimensions, production requirements, and cutting constraints. This reduces material wastage and production costs, promoting sustainability and cost savings.
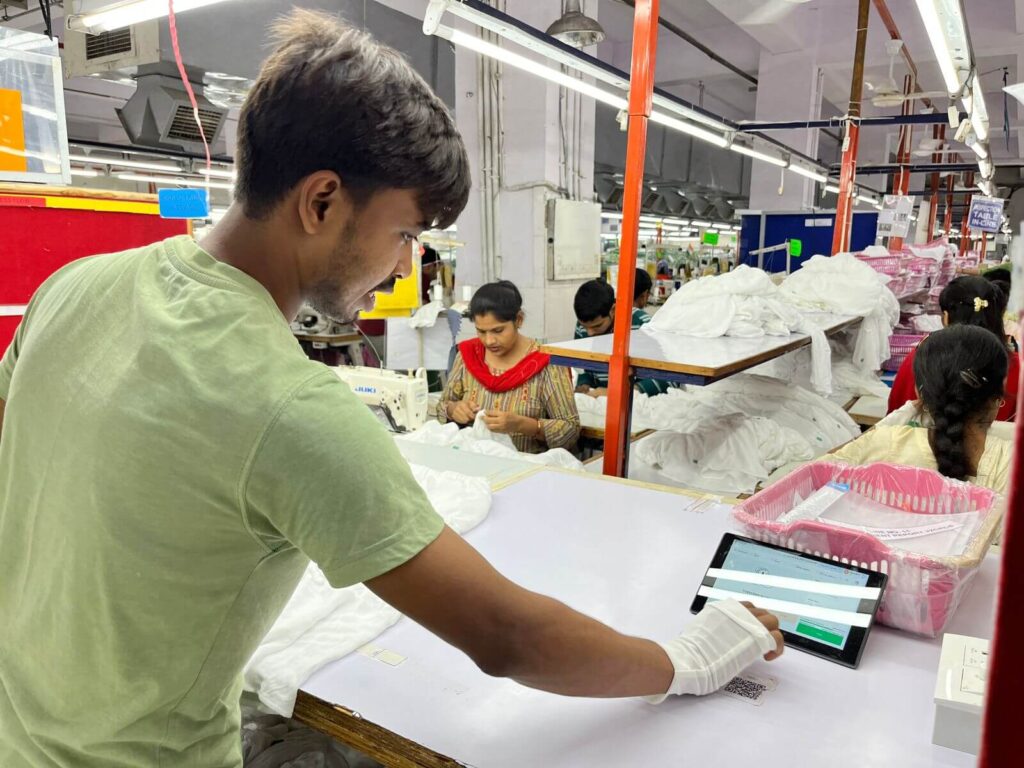
Business Benefits
1) Goodbye to unexpected breakdowns- Stitch machine learning and IoT magic anticipate potential failures, empowering Pee Empro to conduct timely maintenance and minimize unplanned downtime.
2) Improved Workforce Productivity- Stitch helped Pee Empro Exports to unleash the true potential of their workforce by offering real-time insights into productivity and efficiency that helped them to swiftly identify skill gaps and performance bottlenecks.
3) Enhanced Visibility with Stitch Planning Board- Thanks to the Stitch planning board, Pee-Empro gains comprehensive insight into all factory facilities and their available resources. With clear visibility into total booked capacity, available capacity, and total capacity, they now have a holistic view of their production capabilities.