Founded by Vinay Kumar, Basant boasts a sprawling 935,000 sq. ft. state-of-the-art facility, complete with dedicated testing labs, metal fabrication workshops, advanced powder coating lines, and an expansive upholstery unit. Despite their success, Basant recognized the need to embrace Industry 4.0 and digital transformation to unlock their full potential. They needed a way to transform their traditional manufacturing processes into a data-driven, streamlined operation.
Problem Statement
Basant Industries, a leading manufacturer of solid wood furniture, rustic furniture, and industrial furniture, faced several challenges that were hindering their growth and profitability. Like many in the manufacturing industry, they were relying on outdated methods that limited their ability to optimize operations:
- Lack of Real-Time Production Visibility: Imagine managing a vast factory floor with limited real-time insight into your operations. Managers and supervisors were in the dark, unable to track work-in-progress (WIP), machine utilization, or pinpoint potential delays. This lack of shop floor visibility created a reactive rather than proactive environment.
- Manual Data Collection & Spreadsheet Dependency: Picture mountains of paperwork and endless spreadsheets. This was Basant’s reality for data collection, leading to a time-consuming, error-prone process that hindered accurate production analytics. Decisions were often based on guesswork rather than data-driven insights. This hampered their ability to identify cost optimization opportunities and improve operational efficiency.
- Inefficient Production Planning: Production planning was based on intuition and historical data rather than real-time demand and capacity. This resulted in either overproduction (tying up valuable resources) or underproduction (leading to missed deadlines and frustrated customers). Effective capacity planning was a major hurdle.
- Line Balancing Bottlenecks: Workload distribution across production lines was uneven, with some lines overloaded while others sat idle. These line balancing issues created bottlenecks, reduced efficiency, and ultimately impacted production output.
- Inconsistent KPI Monitoring: Without a centralized system to track Key Performance Indicators (KPIs), identifying bottlenecks, measuring improvements, and making data-backed decisions became an uphill battle. They lacked crucial metrics like OEE (Overall Equipment Effectiveness) and needed better performance monitoring.
- Manual Lead Time Tracking & Quality Control: Manually tracking lead times led to inaccurate delivery estimates, potentially damaging customer relationships. They also lacked a standardized system for quality control and compliance, increasing the risk of product defects and customer complaints. They need a robust quality management system (QMS).
- Manual & Paper-Based Data Capturing: Paper-based data collection led to inconsistencies, reporting delays and difficulty in consolidating information. This hindered accurate insights into operations and created difficulty in analyzing data.
- Lack of Digital Data Capture: The absence of digital data capture made it difficult to analyze historical trends, optimize processes, and implement predictive maintenance strategies.
Solutions
- Digitizing Operations- Digitizing manual processes across production lines eliminated paperwork, improved efficiency, and reduced errors. Implemented Stitch to automate shop floor operations and enable data-driven decisions.
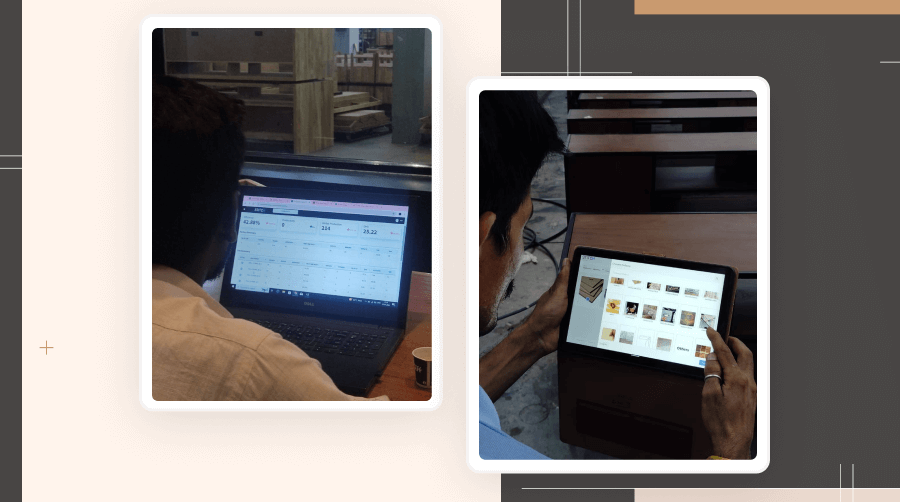
- Standardizing Processes– Industrial engineering studies analysed and optimized processes, pinpointing bottlenecks and boosting productivity. This paved the way for standardized procedures across Basant, ensuring lasting efficiency and sustainability.
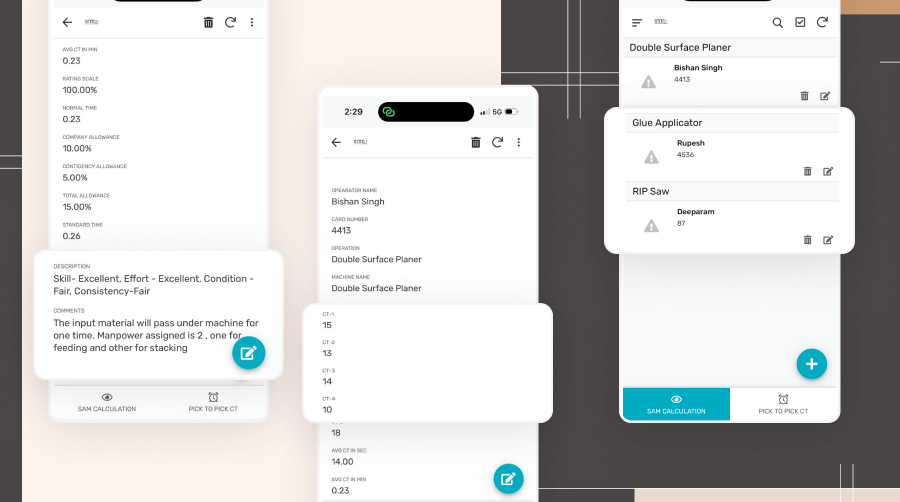
- Sustenance- Stitch dedicated digital team, empowered by comprehensive training, ensures the long-term success of the Stitch system through ongoing maintenance, updates, and continuous improvement.
Project Outcomes
- Enhanced visibility & cutting optimization via defect bulletins and a marker function.
- Customizable inspections and AQL audits were conducted at all production stages.
- Digitization of manual processes improved efficiency and reduced errors.
- Standardized practices increased productivity and consistency.
- Stitch implementation enhanced operational effectiveness.