In the apparel industry, machine breakdowns can be a significant roadblock. They halt the production line, leading to delays affecting delivery timelines and customer satisfaction. Moreover, the downtime caused can inflate operational costs, as every minute of halted production equates to lost revenue.
Picture this: a machine breaks down in the middle of a production run. The cost of repairing or replacing it can be a significant blow to the company’s finances. But that’s not all. In an attempt to make up for lost time, processes are rushed, and the quality of the apparel may suffer. This could potentially tarnish the brand’s reputation, a risk no company can afford to take.
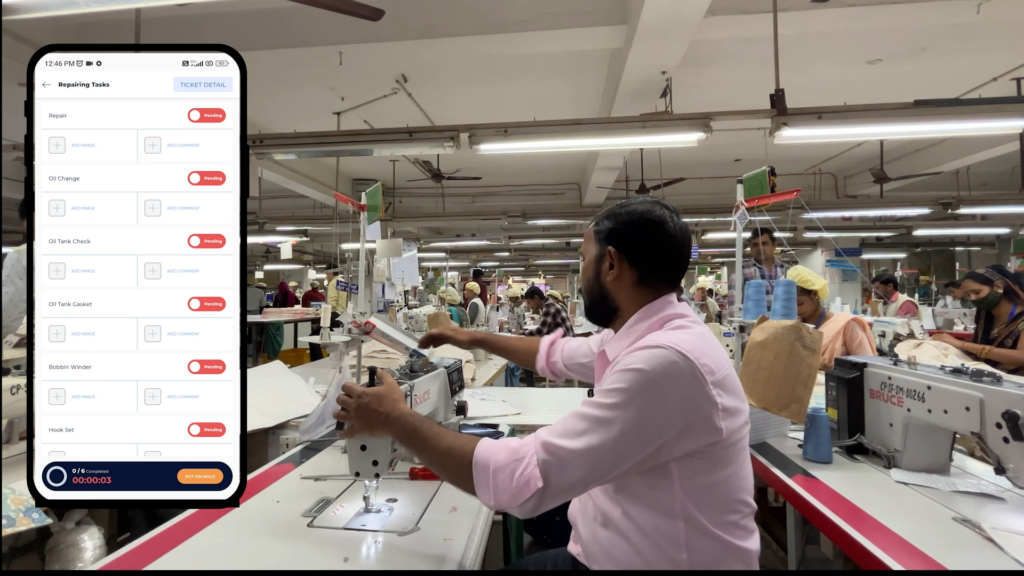
But wait, there’s more. The lack of a spare parts management system brings along its own set of challenges. Let’s delve into these:
- Unplanned Downtime- Without a spare parts management system, a machine breakdown can bring your entire production line to a standstill. The time taken to identify, procure, and replace the faulty part can lead to significant production delays.
- Increased Operational Costs- In the absence of a spare parts management system, you might find yourself ordering parts in panic mode, often paying premium prices. Plus, the cost of machine downtime can quickly escalate, impacting your overall operational costs.
- Inventory Mismanagement- Without a system to efficiently manage your spare parts inventory, you could end up with an excess stock of some parts and a shortage of others. This imbalance can lead to wasted resources and missed repair opportunities.
- Decreased Productivity- Every minute that your machines are idle, your productivity suffers. Delays in procuring spare parts can lead to longer machine downtime, affecting your production targets and delivery timelines.
- Compromised Quality- Extended machine downtime can put pressure on your production schedule, potentially leading to rushed processes when the machine is back up. This can compromise the quality of your apparel, affecting your brand reputation.
In the fast-paced world of apparel manufacturing, a stitch in time, indeed, saves nine. That is why a Stitch team developed a spare management system that can prevent breakdowns. Our system can monitor the machines’ performance in real-time, predict potential issues, and schedule maintenance tasks proactively. This not only minimizes the risk of unexpected breakdowns but also extends the machinery’s lifespan, optimizes production efficiency, and ultimately, safeguards the company’s bottom line.
Spare parts management is like the unsung hero of the apparel industry. It’s the compass that keeps your production ship on course, ensuring smooth sailing even in the roughest of seas. It ensures that your machinery is always up and running, minimizing downtime and maximizing productivity. But why is it so crucial? Let’s delve into it:
- Predictive Maintenance- Imagine being able to foresee a machine breakdown before it happens. With predictive maintenance, this is a reality. By analyzing data from your machines, you can predict when they might need servicing or replacement parts. This proactive approach can save you valuable time and resources.
- Breakdown Maintenance- Despite our best efforts, breakdowns can still occur. But with effective spare parts management, you can ensure that you have the necessary parts on hand to get your machines back up and running as quickly as possible.
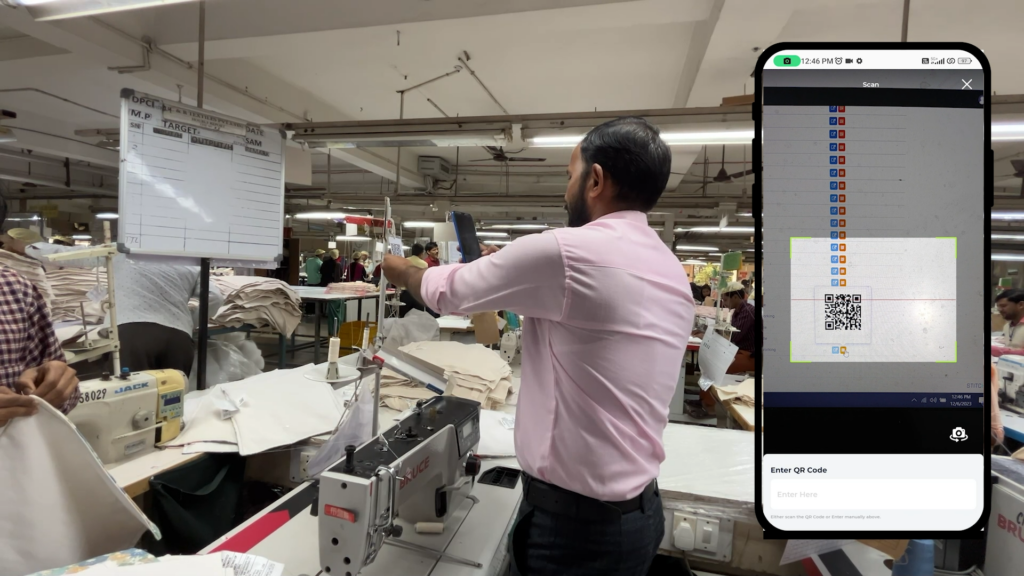
- Warehouse Management Systems- These systems make the entire process easy by generating a request for the needed parts. No more manual searching through your warehouse. With a few clicks, you can locate the parts you need and get your production line back on track.
In essence, spare parts management is not just about having spare parts. It’s about having the right parts, at the right time, in the right place. It’s about turning the tide in your favor in the face of adversity. So, gear up and embrace the power of Stitch Spare Parts Management System in your apparel manufacturing unit today!