Background:
Banswara Syntex is one of Asia’s largest single-mill setups for fiber-dyed yarn, has expanded its reach across more than 50 countries, and is a trusted supplier to renowned fast fashion brands such as Uniqlo, Calvin Klein, Marks and Spencer, and Next. They wanted to achieve a complete shopfloor digital transformation across two factories and 65 production lines.
Prior to implementing STITCH-MES, Banswara relied on a manual system for managing production processes, which often led to inefficiencies, downtime, and quality issues. Recognizing the need for improvement they decided to invest in a digital transformation to streamline operations and enhance overall performance.
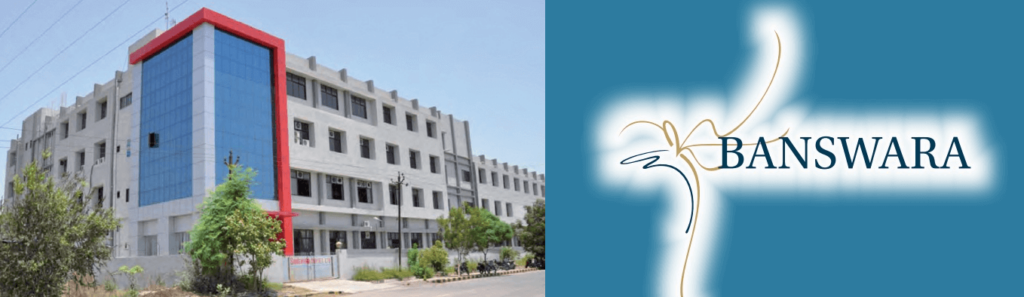
Website- Banswara
Challenges Banswara Syntex Faced
- Incomplete Data Flow: Incomplete data flow across different areas of manufacturing. Without comprehensive data related to production orders, inventory, quality control, maintenance, and other crucial aspects of production. This led to data inconsistencies, manual data entry errors, and a fragmented view of operations, hindering decision-making and overall efficiency.
- Siloed Information: With lack of integrated and comprehensive data from the production floor, information became compartmentalized within different systems or spreadsheets. This siloed approach made it difficult to gather a holistic view of production processes and related data. It became challenging to analyze correlations, identify bottlenecks, and gain insights into the end-to-end manufacturing workflow. Siloed information hampered efficiency, coordination, and the ability to address issues promptly.
- Manual Workarounds: In the absence of digital tools people resort to manual workarounds like using separate spreadsheets, data exports, or manual data entry to transfer information from one person to another. Manual workarounds were time-consuming, error-prone, which led to inconsistencies and delays in data updates. They also led to increased labor costs and decreased productivity.
- Lack of Process Visibility: Manual MIS resulted in a lack of comprehensive process visibility. It becomes challenging to monitor and track the complete lifecycle of orders on the shop floor related to production, quality control, material consumption, maintenance, and other critical parameters. The absence of comprehensive process visibility was a hindrance to real-time decision-making, caused delays, and impacted overall operational efficiency.
- Difficulties in Scaling and Adaptability: With manual process controls in place Baswara faced challenges when it comes to scaling its manufacturing operations to adapt to changing business requirements. As production volumes increased and new processes introduced, the existing system lacked the necessary flexibility to accommodate these changes.
- Missed Opportunities for Optimization: With incomplete or fragmented data, it was difficult to identify areas for improvement, implement performance enhancements, and streamline operations. The absence of an integrated MES was a roadblock to their ability to leverage advanced analytics, automation, and optimization techniques to maximize efficiency and productivity.
How Stitch Solved Their Problem?
Banswara Syntex embarked on a groundbreaking journey by implementing STITCH, a comprehensive manufacturing suite, resulting in a remarkable shopfloor digital transformation. The key project outcomes included:
- STITCH provided real-time visibility into the status of work orders, production progress, and machine utilization thus maintaining visibility and tracking of production activities. STITCH allowed the client to track and monitor the movement of materials, work-in-progress (WIP), and finished goods on the shop floor, ensuring better control and efficient management of production.
- STITCH maintained consistent product quality, which was crucial. STITCH helped address quality-related challenges by enabling real-time monitoring of quality parameters at different stages of production. It facilitated the capture and analysis of quality data, inspection results, defects, and measurements, allowing them to identify deviations, implement corrective actions, and ensure adherence to quality standards. This proactive quality management helped them to reduce defects, rework, and customer complaints.
- STITCH helped the client to effectively plan and schedule their orders in the factories by considering factors like available capacities in different lines and factories. machine availability, skill sets of operators, material availability, and customer demands. By providing accurate production schedules, task assignments, and resource allocation, STITCH helped minimize production delays, improve on-time delivery, and maximize production efficiency.
- STITCH also managed inventory to a great effect. STITCH provided real-time visibility into material consumption, inventory levels, and reorder points. STITCH enabled Banswara to track and manage inventory effectively, ensuring that the required materials are available when needed, reducing production disruptions, and optimizing inventory costs.
- By capturing vast amounts of production data from every process in the entire production cycle, STITCH leveraged that data for performance analysis and continuous improvement initiatives. By analyzing historical and real-time data, Banswara now can identify performance trends, bottlenecks, and areas for improvement. This data-driven approach allows them to make informed decisions, implement process enhancements, optimize resource utilization, and drive operational excellence in garment manufacturing.
- STITCH provided a scalable architecture, allowing them to start and implement the specific modules that align with their operational requirements. This enabled customization and flexibility, ensuring that STITCH can adapt to evolving business needs, accommodate changing production processes, and scale.
Project Outcome
● On the way to 100% paperless factory
● Reduction of over 40% DHU
● Improved Efficiency and Productivity
● Establish Centralized Data Management for factory management.
● Seamless Information Flow
● Enhanced Decision-Making
● Cost Savings and Scalability
● Standardized Processes and Compliance
Client Feedback
“We’re able to foresee problems now, instead of them just popping up all the time. I’ve seen the benefits of astronomical proportions just in terms of a reduction of Defects. Downtime and cost”
— Rahul Bhaduria, Operation Head