FutureFab, founded by Waseem Siddiqui, has three decades of experience sourcing and delivering quality fabrics to exporters & buying houses. Their logistic warehouse spans over 10,000 square feet & serves clients like Target, Marks & Spencer, JCPenney, Bed Bath & Beyond & many more at highly competitive prices. Under the leadership of co-founders Danish Siddiqui & Danish Sharma, Futurefab has embraced sustainability & is disrupting the entire supply chain.
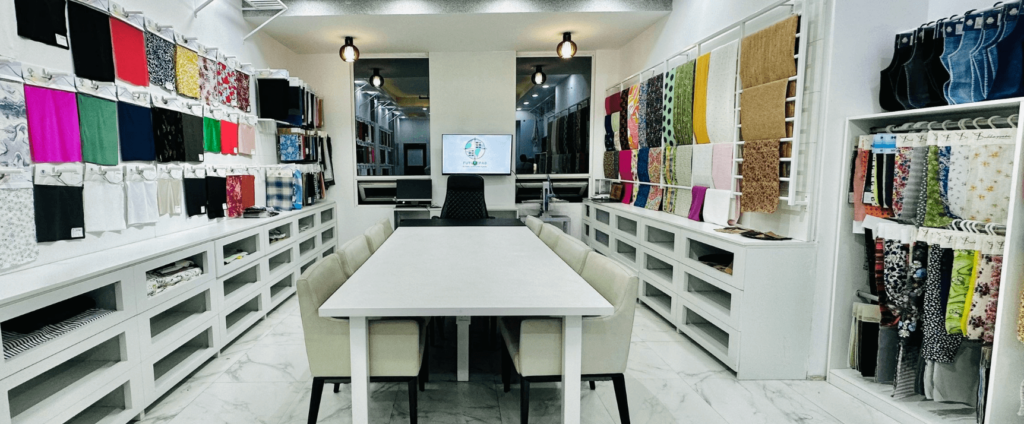
Problem Statement
1. Lack of Visibility in Fabric Tracking- FutureFab lacked visibility when it came to the inventory records in shops and warehouses. Every ingoing and outgoing order was recorded in an excel sheet & was processed through phone call.
2. Manual Requisition Form- FutureFab employees used manual requisition forms, making it difficult to maintain accurate records of all the fabric left once a new order was processed from the inventory.
3. Finding Particular Fabric in the Factory- The FutureFab has a vast inventory, and when a particular swatch is selected, finding a particular fabric becomes difficult, with numerous fabrics stored across various sections and shelves.
Solutions
We implemented the Stitch Warehouse Management System that allowed FutureFab to map the entire warehouse & shop online, and digitize everything in the warehouse further helping them:
1. Efficient Inventory Management- We installed barcodes on every swatch in the shop and to the roll and rack in the warehouses bringing the entire inventory management online that allowed FutureFab to track real-time fabric rolls, ensuring accurate stock levels, and reducing the risk of stockouts or overstocking in the warehouse.
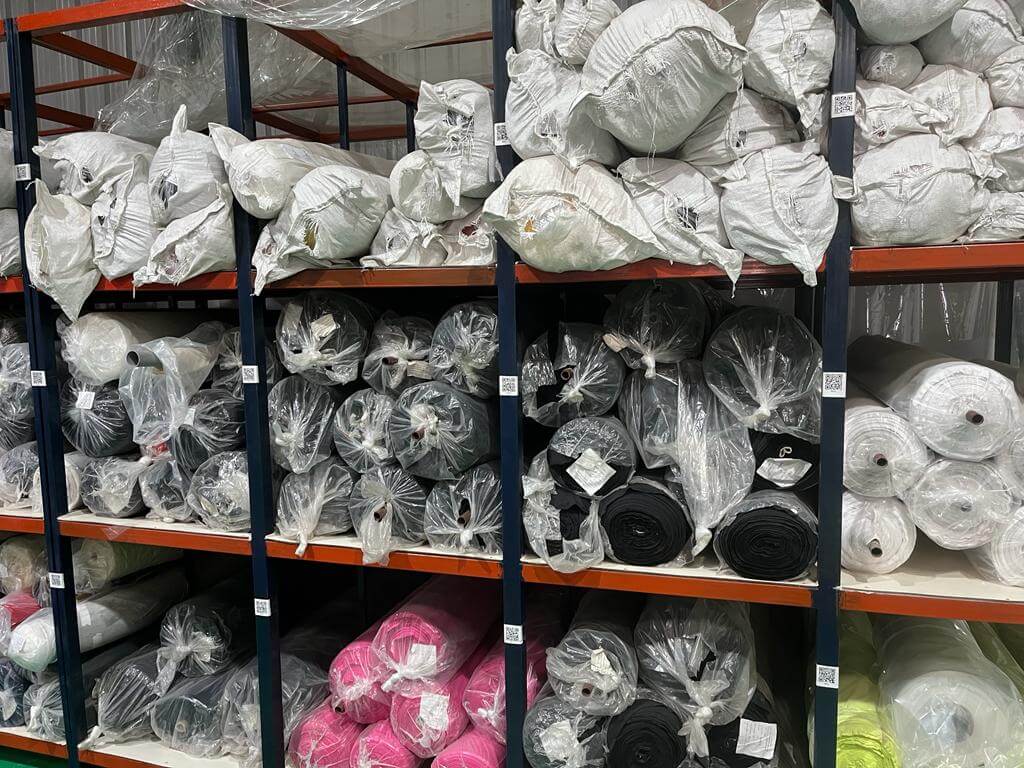
2. Energy Management: STITCH-MES empowered CMV Global to implement advanced energy management systems and monitor energy consumption in real time. This data helped identify energy inefficiencies promptly and implement corrective measures. As a result, CMV Global witnessed a substantial reduction in energy consumption and associated costs, contributing to their environmental and economic sustainability.
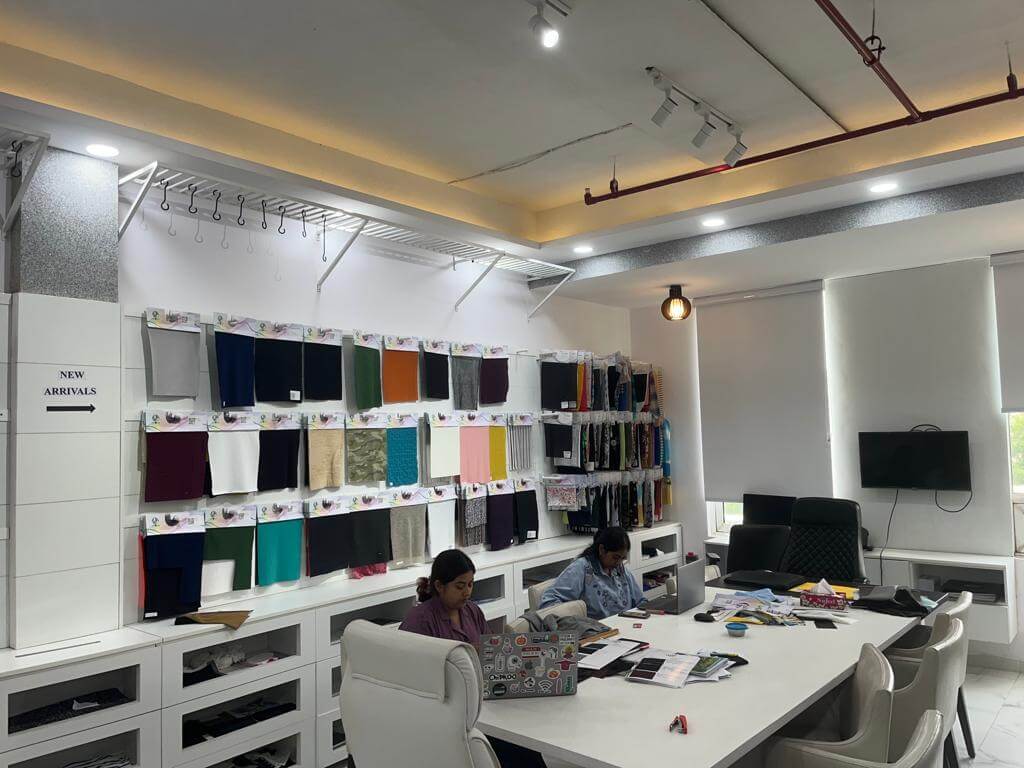
3. Comprehensive Reporting & Easy Order Processing– Stitch WMS provides comprehensive reporting and analytics offering valuable insights into:
- Inventory turnover.
- Popular fabric types.
- Aging of stock items
- Customer demand patterns.
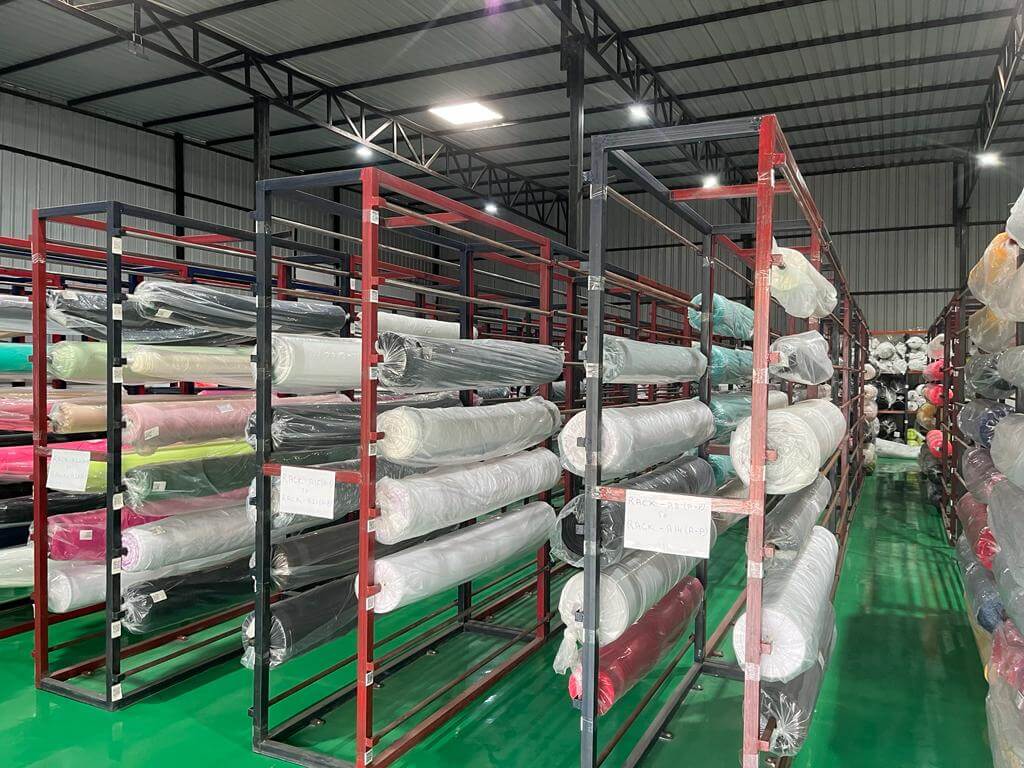
Project Outcomes
1. Enhanced Visibility in Fabric Tracking- The Stitch Warehouse Management System implementation provided FutureFab with improved inventory visibility. They were able to track real-time fabric rolls, ensuring accurate stock levels and overcoming the challenge of constantly updating inventory records in an Excel sheet.
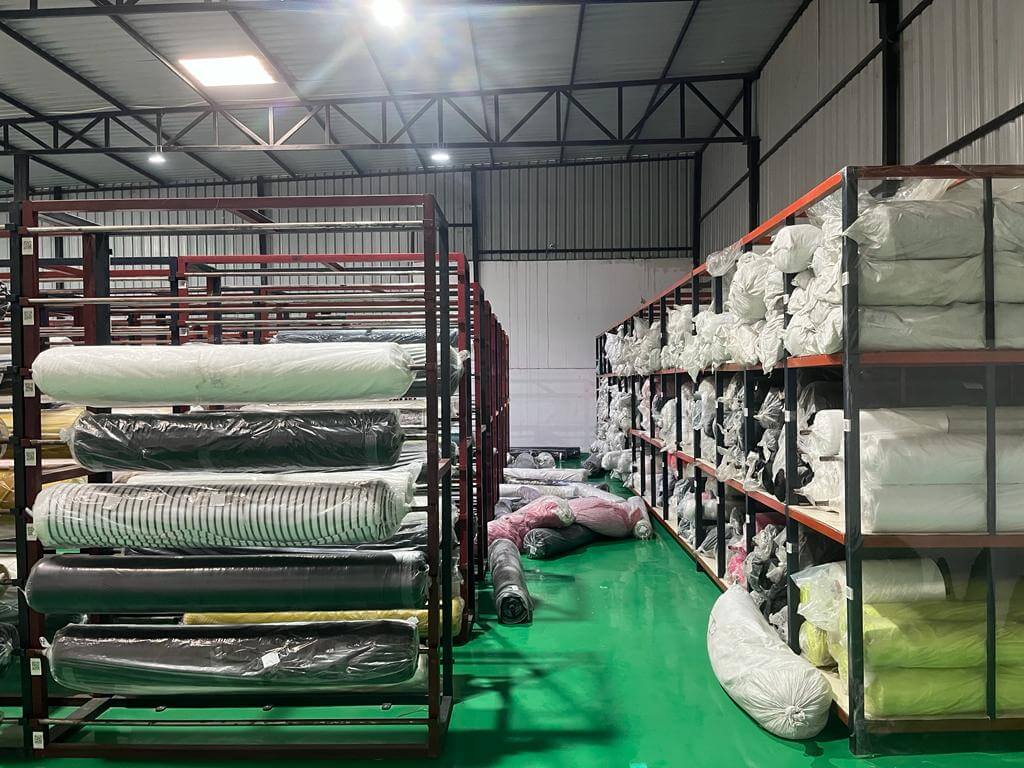
2. Streamlined Requisition Process- By digitizing the requisition process, FutureFab eliminated the manual requisition forms, which had previously made it difficult to maintain accurate records of the remaining fabric after processing new orders.
3. Improved Efficiency in Finding Specific Fabrics- The comprehensive warehouse mapping and inventory digitization allowed FutureFab to easily locate specific fabrics reducing the time and effort spent searching for specific items.
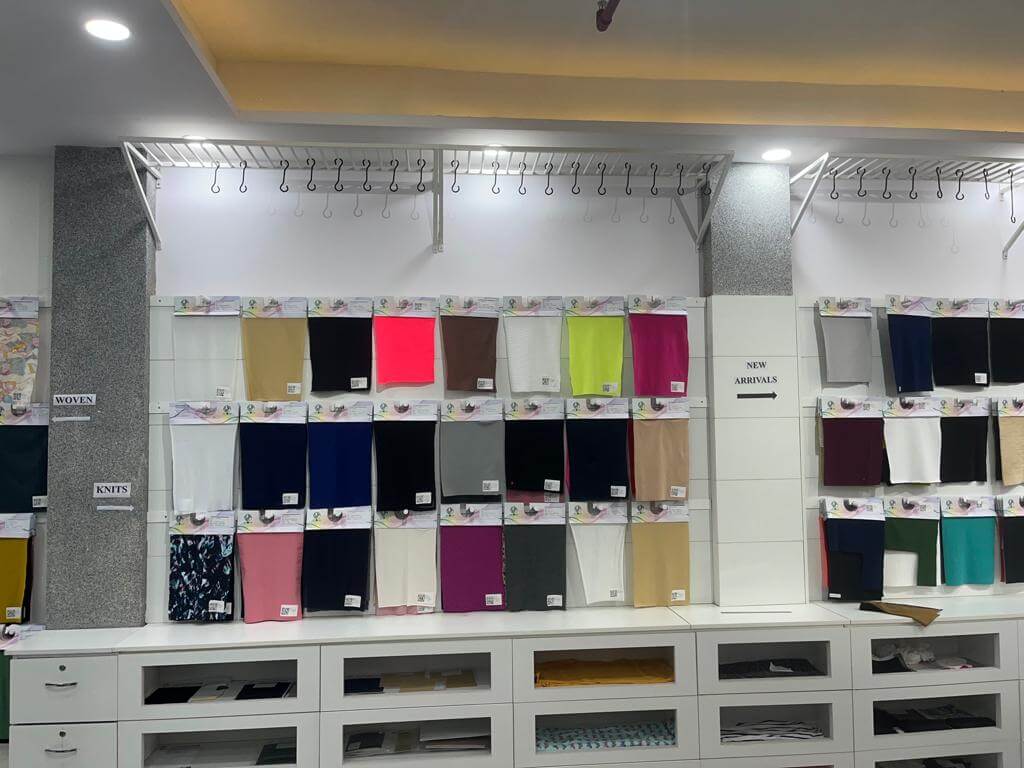
4. Streamlined Order Processing Steps:
- Customer selects the Swatch.
- Fabric expert scans associated QR Codes with that swatch to check stock availability in the warehouse.
- The request is automatically forwarded to the warehouse team with an online requisition slip.
- The warehouse team issues the fabric against the slip to the showroom & the stock is updated accordingly.